Imagine a world without mountains of paperwork where manufacturing and logistics run smoothly. That dream is now becoming a reality, because of technology in Manufacturing Industry.
From managing documents digitally to collaborating in real-time, receiving automated alerts, using mobile devices, and making data-driven decisions, technology is revolutionizing manufacturing and logistic communications.
By adopting digital solutions, manufacturing companies can streamline their processes, improve efficiency, and reduce their reliance on paper-based communication.
Are you ready to dive into the incredible space of paperless possibilities? Let’s begin
Here are five key use cases of technology in manufacturing industry communications
1. Management of Electronic Documents
Manufacturing companies can go paperless by scanning and managing their papers online with the help of technology. Secure cloud-based solutions can store crucial documents including product specs, work orders, and online invoices.
This enables simple access, prompt retrieval, and effective sharing amongst many teams and departments. It decreases the chance of document loss or damage and does away with the necessity for physical storage space.
2. VoIP Communications
Coordination between numerous stakeholders, including designers, engineers, suppliers, and production teams, is common in manufacturing communications.
Through digital platforms and project management tools, technology enables real-time communication.
These solutions such as VoIP provide smooth communication regardless of geographic location by facilitating instant messaging, file sharing, and virtual meetings.
This enhances productivity, quickens the decision-making process, and reduces production process delays.
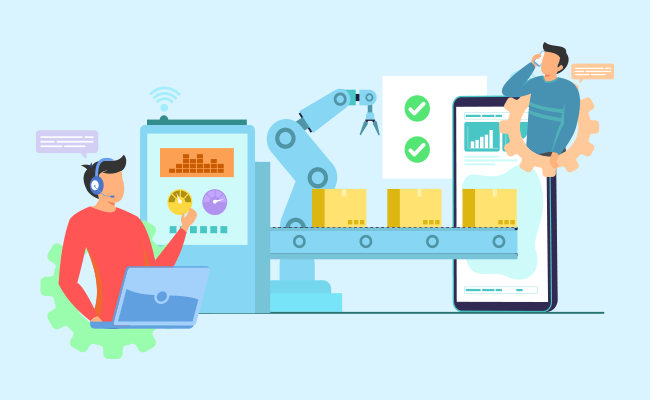
Perks of VoIP include
- VoIP systems can interface with the current communication infrastructure, including PCs, smartphones, and IP-enabled devices.
- Employees can make and receive calls using a variety of devices due to this integration, which enables smooth manufacturing communication across many platforms.
- VoIP systems offer advanced features that improve logistics communications. Some of the functions offered by VoIP technology include call forwarding, call recording, voicemail-to-email transcription, and auto-attendant capabilities.
- By enhancing efficiency, call management, and communication documentation, these capabilities lessen the need for manual note-taking or reliance on paper-based options.
- While planning production plans, talking about project updates, or running online training sessions, VoIP is quite helpful. It lessens the necessity for face-to-face meetings and associated paper-based resources.
3. Automated Alerts and Notifications
In the manufacturing industry, logistic communications are critical for ensuring the timely delivery of raw materials, components, and finished goods.
Due to technology like IVR system, all parties can receive automated alerts and notifications concerning shipments, inventory levels, and production milestones.
This lessens downtime, avoids bottlenecks, and enables proactive decision-making based on real-time information.
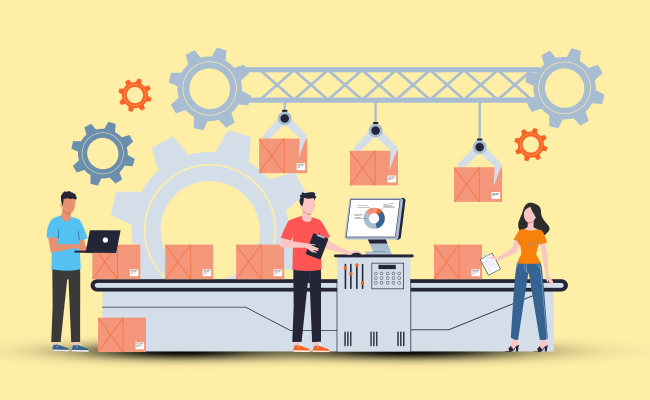
Let us explore the application of IVR technology in manufacturing Industry and logistic communications
a) Streamlined Customer Assistance
Automated IVR systems provide quick access to product information, order status, and technical help, reducing the need for manual assistance and printed manuals.
b) Order Tracking and Status Updates
IVR technology allows customers and partners to track orders and receive real-time updates without relying on manual tracking forms or paper-based communication.
c) Messages and Reminders
IVR number send automatic reminders and notifications to staff, suppliers, and clients, increasing productivity and reducing the need for written notes.
d) Effective Internal Communication
Manufacturing companies use IVR technology for internal communication, such as accessing corporate information, leaving requests, and receiving training updates, minimising the use of internal memos.
e) Surveys and Feedback
It enables manufacturing companies to conduct automated surveys and gather customer feedback, streamlining data collection and evaluation without the need for paper surveys.
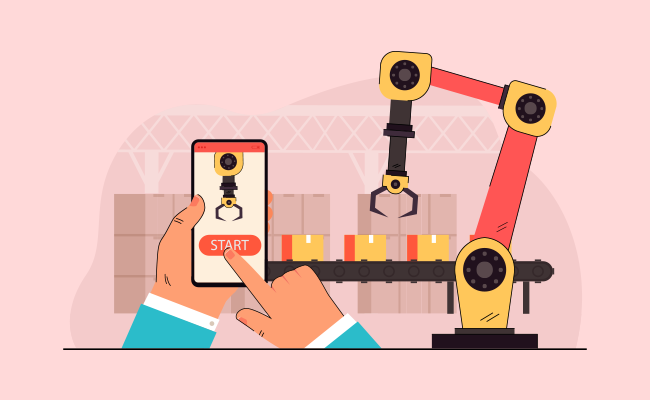
4. Mobile Communication with WhatsApp
Our daily lives now include mobile devices, and their use in manufacturing industry communications has numerous benefits.
Employees may access vital data, connect with coworkers, and report difficulties from the manufacturing floor using smartphones or tablets.
Mobile apps like WhatsApp boost productivity and lessen reliance on paper-based processes by providing quick updates on inventory, production plans, and quality control procedures.
Here is how WhatsApp may be used for manufacturing and logistic communications.
a) Instant Messaging
WhatsApp offers a practical platform for instant messaging that makes it possible for team members, vendors, and clients to communicate quickly and directly.
Real-time communication is possible for crucial messages like production schedules, inventory updates, and logistical information.
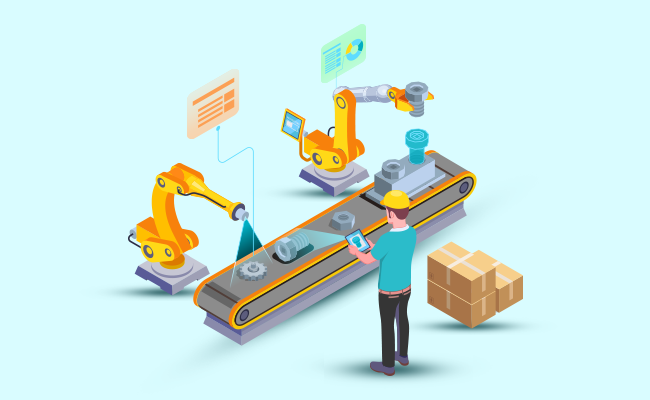
b) Group Chats
WhatsApp’s ability to create group chats makes it simpler to communicate with numerous stakeholders at once.
For effective collaboration and to keep everyone informed, manufacturing businesses can create groups for certain departments or projects.
Group chats are especially helpful for logistic communications since they let distributors, suppliers, and transportation partners stay in touch and easily communicate updates.
c) File Sharing
WhatsApp allows users to share a variety of files, including images, documents, and videos.
This feature is useful for exchanging product specifications, quality control reports, and logistical papers quickly in the manufacturing industry.
Direct file sharing within discussions eliminates the necessity for printing or physical document delivery.
d) Calls Over Voice and Video
WhatsApp offers an alternative to conventional phone calls by enabling voice and video communications.
While addressing intricate production concerns or debugging technological difficulties, this function enables straightforward and timely communication, which is extremely helpful.
Video calls can help virtual meetings run more smoothly by enabling participants to share screens for presentations or visually demonstrate products.
e) Broadcast Lists
Using WhatsApp’s broadcast list feature, manufacturing companies can deliver messages to a lot of recipients at once.
This function is very helpful for distributing major modifications, company-wide announcements, or logistic communications.
It reduces the possibility of misunderstandings by ensuring that everyone receives the information promptly and accurately.
By embracing this technology, the industrial sector may increase cooperation, streamline processes, and create a more sustainable and paperless workplace.
Maximize your Outreach with Voice Broadcasting Feature
Reach more, engage better

5. Analytics and Reporting for Data
Manufacturing businesses may now collect, examine, and use data to make wise decisions with the help of technology in Manufacturing Industry.
Advanced analytics solutions such as contact center software can handle enormous volumes of data, producing insightful information on resource allocation, production efficiency, and quality control.
Management can track key performance indicators, pinpoint areas for improvement, and make data-driven decisions with the help of real-time dashboards and reports.
The Result?
Well it promotes
- Paper waste reduction
- Operational efficiency improvement
- Ongoing process optimization
For managing communication channels like voice calls, emails, and chat, cloud contact centers offer a centralized platform.
This makes it possible for manufacturing firms to efficiently respond to consumer queries, handle logistical issues, and manage internal communications. Digital records of all interactions replace paper documentation and physical documents.
Manufacturers can also track and evaluate communication performance due to the real-time analytics and reporting tools offered by cloud contact centers.
It is possible to track and gauge important parameters like call volume, response times, and customer satisfaction.
With the help of this data-driven methodology, businesses may pinpoint areas for enhancement, streamline procedures, and reach wise conclusions, ultimately cutting down on wasteful paper usage and inefficiencies.
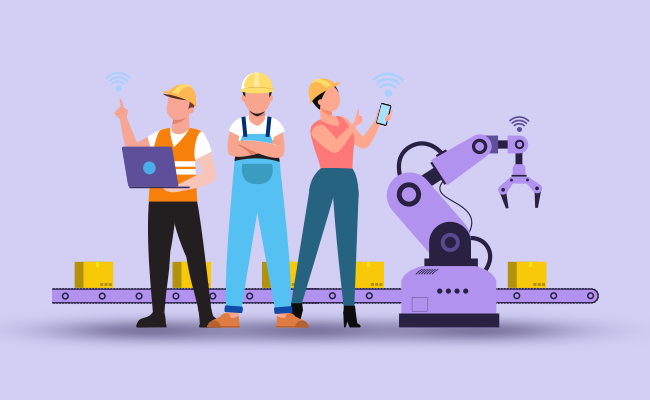
In a nutshell, technology has revolutionized manufacturing and logistic communications, offering a variety of benefits and setting up the foundation for a paperless world.
Manufacturers may increase communication, minimize paper use, streamline processes, and make data-driven choices by adopting the digital solutions outlined above.
Adopting technological advances for manufacturing and logistical communications is a significant step toward a more efficient and ecologically conscious future.